La technologie de découpage en dés de plaquettes, en tant qu’étape critique du processus de fabrication des semi-conducteurs, est directement liée aux performances, au rendement et aux coûts de production des puces.
#01 Contexte et importance du découpage en tranches
1.1 Définition du découpage en dés de plaquettes
Le découpage en dés des plaquettes (également appelé rayage) est une étape essentielle de la fabrication des semi-conducteurs. Il vise à diviser les plaquettes traitées en plusieurs puces individuelles. Ces puces contiennent généralement l'intégralité des fonctionnalités du circuit et constituent les composants clés utilisés dans la production des appareils électroniques. Face à la complexité croissante des puces et à la réduction constante de leurs dimensions, les exigences de précision et d'efficacité de la technologie de découpage en dés des plaquettes deviennent de plus en plus strictes.
En pratique, le découpage des plaquettes utilise généralement des outils de haute précision, tels que des lames diamantées, pour garantir l'intégrité et la fonctionnalité de chaque puce. Les étapes clés comprennent la préparation avant la découpe, le contrôle précis pendant la découpe et le contrôle qualité après la découpe.
Avant la découpe, la plaquette doit être marquée et positionnée afin de garantir des trajectoires de coupe précises. Pendant la découpe, des paramètres tels que la pression et la vitesse de l'outil doivent être strictement contrôlés afin d'éviter d'endommager la plaquette. Après la découpe, des contrôles qualité complets sont effectués pour garantir que chaque puce répond aux normes de performance.
Les principes fondamentaux de la technologie de découpage en dés de plaquettes englobent non seulement le choix de l'équipement de découpe et le réglage des paramètres du procédé, mais aussi l'influence des propriétés mécaniques et des caractéristiques des matériaux sur la qualité de la découpe. Par exemple, les plaquettes de silicium à faible constante diélectrique, en raison de leurs propriétés mécaniques inférieures, sont très sensibles à la concentration de contraintes lors de la découpe, ce qui entraîne des défaillances telles que l'écaillage et la fissuration. La faible dureté et la fragilité des matériaux à faible constante diélectrique les rendent plus vulnérables aux dommages structurels sous l'effet de contraintes mécaniques ou thermiques, notamment lors de la découpe. Le contact entre l'outil et la surface de la plaquette, associé à des températures élevées, peut accentuer encore la concentration de contraintes.
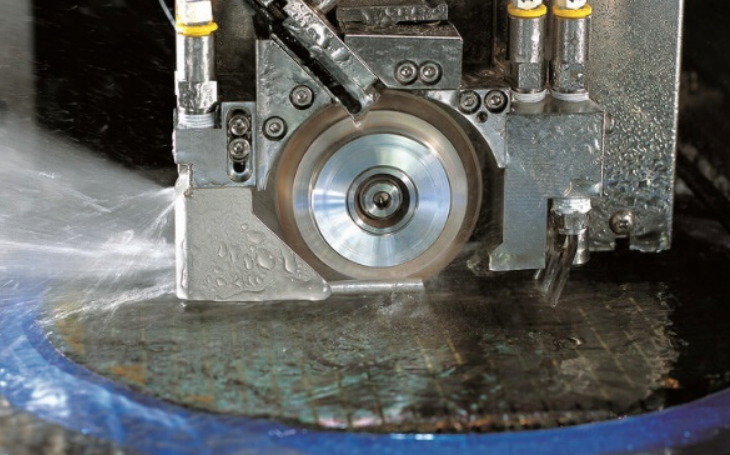
Grâce aux progrès de la science des matériaux, la technologie de découpage en dés de plaquettes s'est étendue au-delà des semi-conducteurs traditionnels à base de silicium pour inclure de nouveaux matériaux comme le nitrure de gallium (GaN). Ces nouveaux matériaux, en raison de leur dureté et de leurs propriétés structurelles, posent de nouveaux défis aux procédés de découpage en dés, nécessitant de nouvelles améliorations des outils et techniques de coupe.
En tant que processus critique dans l'industrie des semi-conducteurs, le découpage en dés des plaquettes continue d'être optimisé en réponse à l'évolution des demandes et aux avancées technologiques, jetant les bases des futures technologies de la microélectronique et des circuits intégrés.
Les améliorations apportées à la technologie de découpage en dés des plaquettes vont au-delà du développement de matériaux et d'outils auxiliaires. Elles englobent également l'optimisation des procédés, l'amélioration des performances des équipements et le contrôle précis des paramètres de découpage. Ces avancées visent à garantir une précision, une efficacité et une stabilité élevées du processus de découpage en dés des plaquettes, répondant ainsi aux besoins de l'industrie des semi-conducteurs en termes de dimensions réduites, d'intégration accrue et de structures de puces plus complexes.
Zone d'amélioration | Mesures spécifiques | Effets |
Optimisation des processus | - Améliorer les préparations initiales, telles qu'un positionnement plus précis des plaquettes et une planification du trajet. | - Réduit les erreurs de coupe et améliore la stabilité. |
- Minimise les erreurs de coupe et améliore la stabilité. | - Adoptez des mécanismes de surveillance et de rétroaction en temps réel pour ajuster la pression, la vitesse et la température de l'outil. | |
- Réduisez les taux de casse des plaquettes et améliorez la qualité des puces. | ||
Amélioration des performances des équipements | - Utiliser des systèmes mécaniques de haute précision et une technologie de contrôle d'automatisation avancée. | - Améliore la précision de coupe et réduit le gaspillage de matériaux. |
- Introduire une technologie de découpe laser adaptée aux plaquettes de matériaux à haute dureté. | - Améliorer l’efficacité de la production et réduire les erreurs manuelles. | |
- Augmenter l'automatisation des équipements pour une surveillance et des réglages automatiques. | ||
Contrôle précis des paramètres | - Ajustez finement les paramètres tels que la profondeur de coupe, la vitesse, le type d'outil et les méthodes de refroidissement. | - Assurer l'intégrité de la matrice et les performances électriques. |
- Personnalisez les paramètres en fonction du matériau, de l'épaisseur et de la structure de la plaquette. | - Augmentez les taux de rendement, réduisez le gaspillage de matériaux et diminuez les coûts de production. | |
Importance stratégique | - Explorer en permanence de nouvelles voies technologiques, optimiser les processus et améliorer les capacités des équipements pour répondre aux demandes du marché. | - Améliorer le rendement et les performances de fabrication des puces, en soutenant le développement de nouveaux matériaux et de conceptions de puces avancées. |
1.2 L'importance du découpage en tranches
Le découpage des plaquettes joue un rôle essentiel dans le processus de fabrication des semi-conducteurs, impactant directement les étapes ultérieures ainsi que la qualité et les performances du produit final. Son importance peut être détaillée comme suit :
Premièrement, la précision et la régularité du découpage sont essentielles pour garantir le rendement et la fiabilité des puces. Lors de leur fabrication, les plaquettes subissent de multiples étapes de traitement pour former de nombreuses structures de circuits complexes, qui doivent être découpées avec précision en puces individuelles (matrices). Des erreurs importantes d'alignement ou de découpe lors du découpage peuvent endommager les circuits, affectant ainsi la fonctionnalité et la fiabilité de la puce. Par conséquent, une technologie de découpage haute précision garantit non seulement l'intégrité de chaque puce, mais prévient également l'endommagement des circuits internes, améliorant ainsi le rendement global.
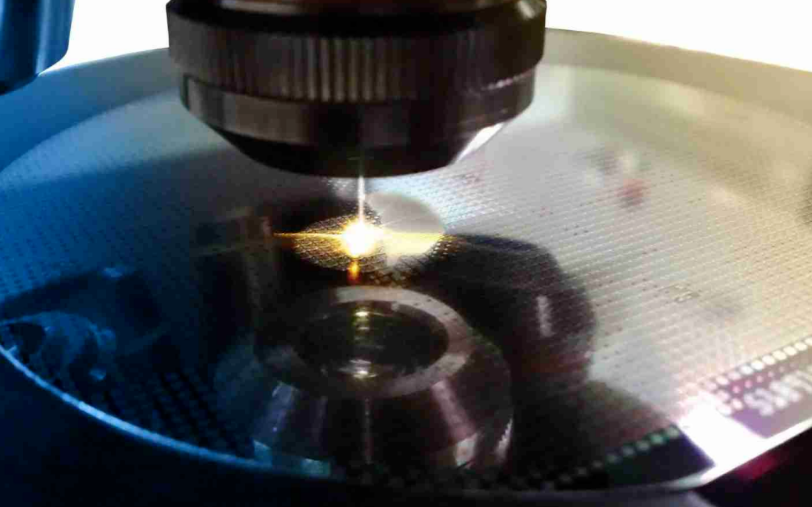
Deuxièmement, le découpage des plaquettes a un impact significatif sur l'efficacité de la production et la maîtrise des coûts. Étape cruciale du processus de fabrication, son efficacité influence directement la progression des étapes suivantes. L'optimisation du processus de découpage, l'augmentation des niveaux d'automatisation et l'amélioration des vitesses de découpe permettent d'améliorer considérablement l'efficacité globale de la production.
D'autre part, le gaspillage de matière lors du découpage est un facteur critique de gestion des coûts. L'utilisation de technologies de découpage avancées réduit non seulement les pertes de matière inutiles lors du processus de découpe, mais augmente également l'utilisation des plaquettes, diminuant ainsi les coûts de production.
Avec les progrès de la technologie des semi-conducteurs, le diamètre des plaquettes continue d'augmenter, tout comme la densité des circuits, ce qui impose des exigences accrues aux technologies de découpage en dés. Les plaquettes plus grandes nécessitent un contrôle plus précis des trajectoires de découpe, notamment dans les zones de circuits à haute densité, où même des écarts mineurs peuvent rendre plusieurs puces défectueuses. De plus, les plaquettes plus grandes impliquent davantage de lignes de découpe et des étapes de processus plus complexes, ce qui nécessite des améliorations supplémentaires en termes de précision, de régularité et d'efficacité des technologies de découpage en dés pour relever ces défis.
1.3 Processus de découpage des plaquettes
Le processus de découpage des plaquettes comprend toutes les étapes, de la préparation au contrôle qualité final. Chaque étape est essentielle pour garantir la qualité et les performances des puces découpées. Vous trouverez ci-dessous une explication détaillée de chaque phase.
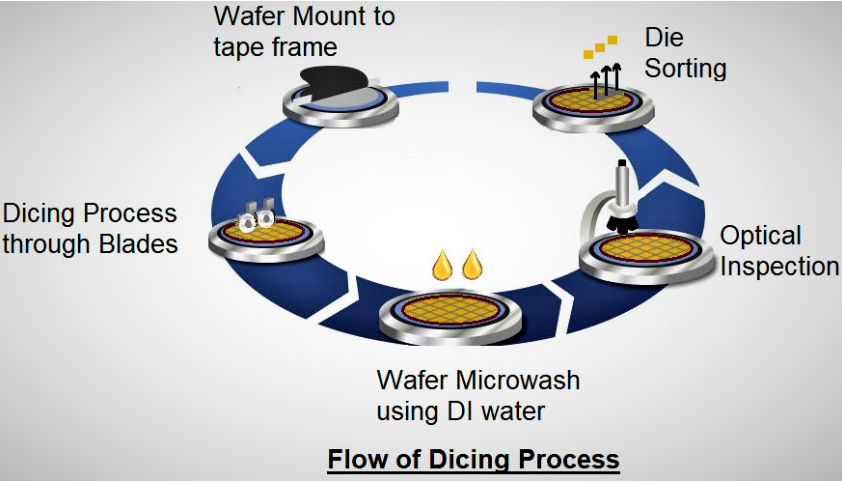
Phase | Description détaillée |
Phase de préparation | -Nettoyage des plaquettes:Utilisez de l'eau de haute pureté et des agents de nettoyage spécialisés, combinés à un nettoyage ultrasonique ou mécanique, pour éliminer les impuretés, les particules et les contaminants, garantissant ainsi une surface propre. -Positionnement précis:Utilisez un équipement de haute précision pour garantir que la plaquette est divisée avec précision le long des chemins de coupe conçus. -Fixation de plaquettes:Fixez la plaquette sur un cadre en ruban pour maintenir la stabilité pendant la coupe, évitant ainsi les dommages causés par les vibrations ou les mouvements. |
Phase de coupe | -Découpe à la lame:Utilisez des lames diamantées rotatives à grande vitesse pour la découpe physique, adaptées aux matériaux à base de silicium et rentables. -Découpage au laser:Utilisez des faisceaux laser à haute énergie pour une découpe sans contact, idéale pour les matériaux cassants ou à haute dureté comme le nitrure de gallium, offrant une plus grande précision et moins de perte de matière. -Nouvelles technologies:Introduire des technologies de découpe laser et plasma pour améliorer encore l’efficacité et la précision tout en minimisant les zones affectées par la chaleur. |
Phase de nettoyage | - Utilisez de l'eau déionisée (eau DI) et des agents de nettoyage spécialisés, combinés à un nettoyage par ultrasons ou par pulvérisation, pour éliminer les débris et la poussière générés pendant la coupe, empêchant les résidus d'affecter les processus ultérieurs ou les performances électriques des puces. - L'eau DI de haute pureté évite l'introduction de nouveaux contaminants, garantissant un environnement de plaquette propre. |
Phase d'inspection | -Inspection optique:Utilisez des systèmes de détection optique combinés à des algorithmes d'IA pour identifier rapidement les défauts, garantissant l'absence de fissures ou d'écaillages dans les copeaux coupés en dés, améliorant l'efficacité de l'inspection et réduisant les erreurs humaines. -Mesure des dimensions: Vérifiez que les dimensions de la puce correspondent aux spécifications de conception. -Tests de performance électrique:Assurez-vous que les performances électriques des puces critiques répondent aux normes, garantissant ainsi la fiabilité des applications ultérieures. |
Phase de tri | - Utilisez des bras robotisés ou des ventouses à vide pour séparer les puces qualifiées du cadre de la bande et les trier automatiquement en fonction des performances, garantissant ainsi l'efficacité et la flexibilité de la production tout en améliorant la précision. |
Le processus de découpe de plaquettes comprend le nettoyage, le positionnement, la découpe, l'inspection et le tri des plaquettes, chaque étape étant cruciale. Grâce aux progrès de l'automatisation, de la découpe laser et des technologies d'inspection par IA, les systèmes modernes de découpe de plaquettes permettent d'atteindre une précision et une vitesse accrues, tout en réduisant les pertes de matière. À l'avenir, de nouvelles technologies de découpe, telles que le laser et le plasma, remplaceront progressivement la découpe traditionnelle à la lame pour répondre aux besoins de conceptions de puces de plus en plus complexes, stimulant ainsi le développement des procédés de fabrication des semi-conducteurs.
Technologie de découpe de plaquettes et ses principes
L'image illustre trois technologies courantes de découpe de plaquettes :Découpe à la lame,Découpage au laser, etDécoupage au plasmaVous trouverez ci-dessous une analyse détaillée et une explication supplémentaire de ces trois techniques :
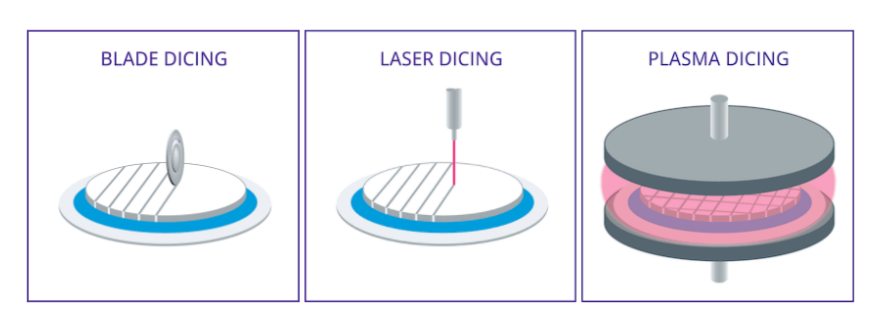
Dans la fabrication de semi-conducteurs, la découpe des plaquettes est une étape cruciale qui nécessite de choisir la méthode de découpe appropriée en fonction de l'épaisseur de la plaquette. La première étape consiste à déterminer l'épaisseur de la plaquette. Si l'épaisseur de la plaquette dépasse 100 microns, la découpe par lame peut être choisie. Si la découpe par lame ne convient pas, la méthode de découpe par fracture peut être utilisée, qui comprend à la fois la découpe par rayage et la découpe par lame.
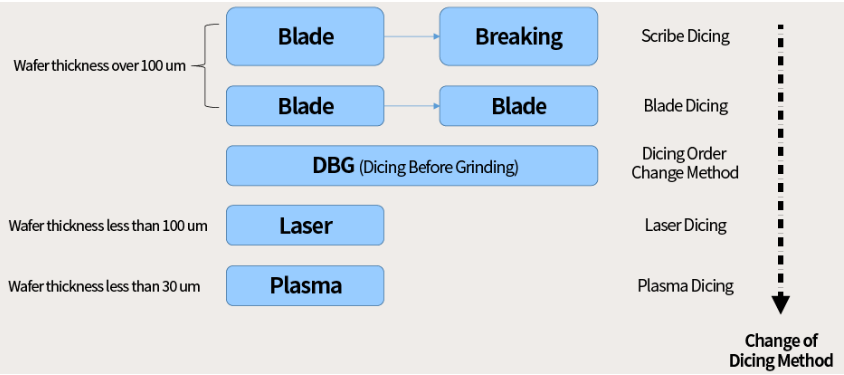
Lorsque l'épaisseur de la plaquette est comprise entre 30 et 100 microns, la méthode DBG (Dice Before Grinding) est recommandée. Dans ce cas, la découpe par rayage, le découpage à la lame ou l'ajustement de la séquence de découpe peuvent être choisis pour obtenir les meilleurs résultats.
Pour les wafers ultra-minces d'une épaisseur inférieure à 30 microns, la découpe laser est la méthode privilégiée, car elle permet de découper des wafers fins avec précision et sans endommager excessivement. Si la découpe laser ne répond pas à des exigences spécifiques, la découpe plasma peut être utilisée comme alternative. Ce schéma fournit un guide de décision clair pour garantir le choix de la technologie de découpe de wafer la plus adaptée à différentes épaisseurs.
2.1 Technologie de coupe mécanique
La découpe mécanique est la méthode traditionnelle de découpage des plaquettes. Son principe de base consiste à utiliser une meule diamantée rotative à grande vitesse comme outil de coupe pour découper la plaquette. L'équipement principal comprend une broche à palier pneumatique, qui entraîne la meule diamantée à grande vitesse pour réaliser une découpe ou un rainurage précis selon une trajectoire prédéfinie. Cette technologie est largement utilisée dans l'industrie en raison de son faible coût, de son rendement élevé et de ses nombreuses applications.
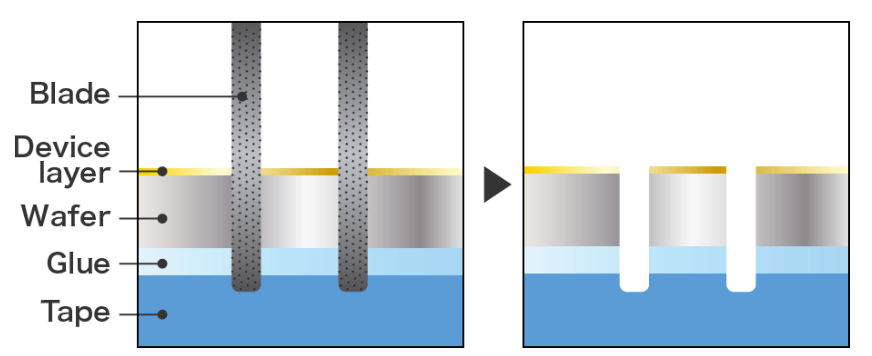
Avantages
La dureté et la résistance à l'usure élevées des meules diamantées permettent à la technologie de découpe mécanique de s'adapter aux exigences de découpe de divers matériaux de plaquettes, qu'il s'agisse de matériaux traditionnels à base de silicium ou de semi-conducteurs composites plus récents. Son fonctionnement est simple et ses exigences techniques relativement faibles renforcent sa popularité en production de masse. De plus, comparée à d'autres méthodes de découpe comme la découpe laser, la découpe mécanique présente des coûts plus maîtrisables, ce qui la rend idéale pour les productions en grande série.
Limites
Malgré ses nombreux avantages, la technologie de découpe mécanique présente également des limites. Premièrement, en raison du contact physique entre l'outil et la plaquette, la précision de découpe est relativement limitée, ce qui entraîne souvent des écarts dimensionnels pouvant affecter la précision du packaging et des tests ultérieurs des puces. Deuxièmement, des défauts tels que l'écaillage et les fissures peuvent facilement apparaître lors de la découpe mécanique, ce qui non seulement affecte le rendement, mais peut également nuire à la fiabilité et à la durée de vie des puces. Les dommages induits par les contraintes mécaniques sont particulièrement préjudiciables à la fabrication de puces haute densité, notamment lors de la découpe de matériaux fragiles, où ces problèmes sont plus importants.
Améliorations technologiques
Pour surmonter ces limitations, les chercheurs optimisent en permanence le processus de coupe mécanique. Parmi les principales améliorations, on compte l'optimisation de la conception et du choix des matériaux des meules afin d'améliorer la précision et la durabilité de la coupe. De plus, l'optimisation de la conception structurelle et des systèmes de contrôle des équipements de coupe a permis d'améliorer encore la stabilité et l'automatisation du processus. Ces avancées réduisent les erreurs humaines et améliorent la régularité des coupes. L'introduction de technologies avancées d'inspection et de contrôle qualité pour la surveillance en temps réel des anomalies pendant le processus de coupe a également considérablement amélioré la fiabilité et le rendement de la coupe.
Développement futur et nouvelles technologies
Bien que la découpe mécanique occupe toujours une place importante dans la découpe des plaquettes, de nouvelles technologies de découpe progressent rapidement à mesure que les procédés de fabrication des semi-conducteurs évoluent. Par exemple, l'application de la découpe laser thermique apporte de nouvelles solutions aux problèmes de précision et de défauts de la découpe mécanique. Cette méthode de découpe sans contact réduit les contraintes physiques sur la plaquette, diminuant ainsi considérablement l'incidence de l'écaillage et des fissures, notamment lors de la découpe de matériaux plus fragiles. À l'avenir, l'intégration de la découpe mécanique aux techniques de découpe émergentes offrira davantage d'options et de flexibilité à la fabrication de semi-conducteurs, améliorant ainsi l'efficacité de la production et la qualité des puces.
En conclusion, bien que la technologie de découpe mécanique présente certains inconvénients, les améliorations technologiques continues et son intégration avec de nouvelles techniques de découpe lui permettent de continuer à jouer un rôle important dans la fabrication de semi-conducteurs et de maintenir sa compétitivité dans les processus futurs.
2.2 Technologie de découpe laser
La découpe laser, nouvelle méthode de découpe de plaquettes, a progressivement gagné en popularité dans l'industrie des semi-conducteurs grâce à sa haute précision, l'absence de dommages par contact mécanique et sa rapidité de découpe. Cette technologie exploite la haute densité énergétique et la capacité de focalisation d'un faisceau laser pour créer une petite zone affectée thermiquement à la surface du matériau de la plaquette. Lorsque le faisceau laser est appliqué sur la plaquette, la contrainte thermique générée provoque la fracture du matériau à l'endroit prévu, permettant une découpe précise.
Avantages de la technologie de découpe laser
• Haute précision:La capacité de positionnement précis du faisceau laser permet une précision de découpe de l'ordre du micron, voire du nanomètre, répondant aux exigences de la fabrication moderne de circuits intégrés de haute précision et de haute densité.
• Aucun contact mécanique:La découpe laser évite le contact physique avec la plaquette, évitant ainsi les problèmes courants de découpe mécanique, tels que l'écaillage et la fissuration, améliorant considérablement le taux de rendement et la fiabilité des puces.
• Vitesse de coupe rapide:La vitesse élevée de la découpe laser contribue à accroître l'efficacité de la production, la rendant particulièrement adaptée aux scénarios de production à grande échelle et à grande vitesse.
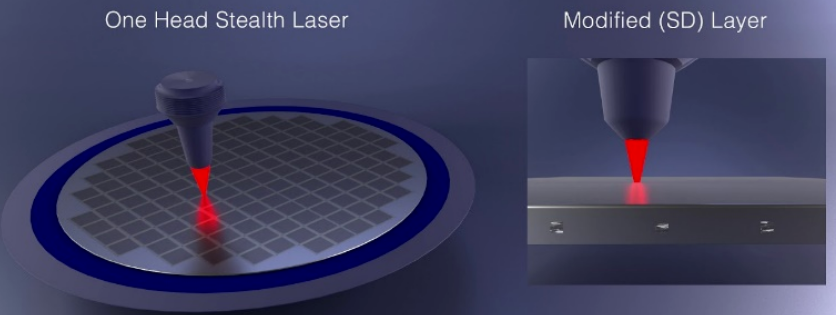
Défis rencontrés
• Coût élevé de l'équipement:L'investissement initial pour les équipements de découpe laser est élevé, ce qui présente une pression économique, en particulier pour les petites et moyennes entreprises de production.
• Contrôle des processus complexes:La découpe laser nécessite un contrôle précis de plusieurs paramètres, notamment la densité énergétique, la position de mise au point et la vitesse de découpe, ce qui rend le processus complexe.
• Problèmes liés à la zone affectée par la chaleurBien que la découpe laser sans contact réduise les dommages mécaniques, la contrainte thermique induite par la zone affectée thermiquement (ZAT) peut avoir un impact négatif sur les propriétés du matériau de la plaquette. Une optimisation plus poussée du procédé est nécessaire pour minimiser cet effet.
Orientations d'amélioration technologique
Pour relever ces défis, les chercheurs se concentrent sur la réduction des coûts d’équipement, l’amélioration de l’efficacité de coupe et l’optimisation du flux de processus.
• Lasers et systèmes optiques efficaces:En développant des lasers plus efficaces et des systèmes optiques avancés, il est possible de réduire les coûts d’équipement tout en améliorant la précision et la vitesse de coupe.
• Optimisation des paramètres du processus:Des recherches approfondies sur l’interaction entre les lasers et les matériaux des plaquettes sont menées pour améliorer les processus qui réduisent la zone affectée par la chaleur, améliorant ainsi la qualité de découpe.
• Systèmes de contrôle intelligents:Le développement de technologies de contrôle intelligentes vise à automatiser et à optimiser le processus de découpe laser, en améliorant sa stabilité et sa cohérence.
La technologie de découpe laser est particulièrement efficace pour les plaquettes ultra-minces et les applications de découpe de haute précision. Face à l'augmentation de la taille des plaquettes et de la densité des circuits, les méthodes de découpe mécanique traditionnelles peinent à répondre aux exigences de haute précision et de rendement élevées de la fabrication moderne des semi-conducteurs. Grâce à ses avantages uniques, la découpe laser s'impose comme la solution privilégiée dans ces domaines.
Bien que la technologie de découpe laser reste confrontée à des défis tels que le coût élevé des équipements et la complexité des procédés, ses avantages uniques en matière de haute précision et de protection contre les dommages sans contact en font un axe de développement important pour la fabrication de semi-conducteurs. Grâce aux progrès constants de la technologie laser et des systèmes de contrôle intelligents, la découpe laser devrait améliorer encore l'efficacité et la qualité de la découpe des plaquettes, stimulant ainsi le développement continu de l'industrie des semi-conducteurs.
2.3 Technologie de découpe plasma
La technologie de découpe plasma, méthode émergente de découpe de plaquettes, a suscité un intérêt considérable ces dernières années. Elle utilise des faisceaux plasma à haute énergie pour découper les plaquettes avec précision en contrôlant l'énergie, la vitesse et la trajectoire de coupe du faisceau plasma, pour des résultats optimaux.
Principe de fonctionnement et avantages
Le procédé de découpe plasma repose sur un faisceau plasma haute température et haute énergie généré par l'équipement. Ce faisceau peut chauffer le matériau de la plaquette jusqu'à son point de fusion ou de vaporisation en très peu de temps, permettant une découpe rapide. Comparée à la découpe mécanique ou laser traditionnelle, la découpe plasma est plus rapide et produit une zone affectée thermiquement plus petite, réduisant ainsi efficacement l'apparition de fissures et de dommages lors de la découpe.
Dans les applications pratiques, la technologie de découpe plasma est particulièrement adaptée à la manipulation de plaquettes de formes complexes. Son faisceau plasma haute énergie et réglable permet de découper facilement des plaquettes de formes irrégulières avec une grande précision. Par conséquent, dans la fabrication microélectronique, notamment pour la production personnalisée et en petites séries de puces haut de gamme, cette technologie est très prometteuse pour une utilisation généralisée.
Défis et limites
Malgré les nombreux avantages de la technologie de découpe plasma, elle est également confrontée à certains défis.
• Processus complexe:Le processus de découpe plasma est complexe et nécessite des équipements de haute précision et des opérateurs expérimentés pour garantirprécision et stabilité dans la coupe.
• Contrôle et sécurité de l'environnement:La nature à haute température et à haute énergie du faisceau de plasma nécessite des mesures de contrôle environnemental et de sécurité strictes, ce qui augmente la complexité et le coût de mise en œuvre.
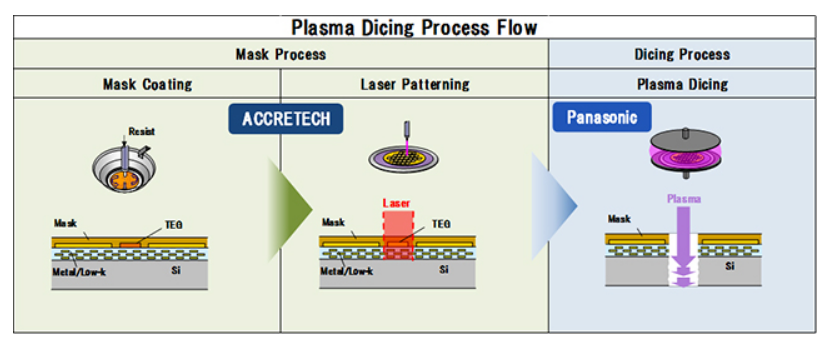
Orientations de développement futures
Grâce aux progrès technologiques, les défis liés à la découpe plasma devraient être progressivement surmontés. Le développement d'équipements de découpe plus intelligents et plus stables permettra de réduire la dépendance aux opérations manuelles, améliorant ainsi l'efficacité de la production. Parallèlement, l'optimisation des paramètres de procédé et de l'environnement de découpe contribuera à réduire les risques de sécurité et les coûts d'exploitation.
Dans l'industrie des semi-conducteurs, les innovations en matière de découpe et de découpage de plaquettes sont essentielles au développement du secteur. La découpe plasma, grâce à sa haute précision, son efficacité et sa capacité à traiter des plaquettes de formes complexes, s'est imposée comme un nouvel acteur majeur dans ce domaine. Bien que des défis subsistent, ceux-ci seront progressivement relevés grâce à l'innovation technologique continue, offrant ainsi de nouvelles possibilités et opportunités à la fabrication de semi-conducteurs.
Les perspectives d'application de la technologie de découpe plasma sont vastes et elle devrait jouer un rôle croissant dans la fabrication de semi-conducteurs à l'avenir. Grâce à une innovation et une optimisation technologiques continues, la découpe plasma permettra non seulement de relever les défis actuels, mais aussi de devenir un puissant moteur de croissance pour l'industrie des semi-conducteurs.
2.4 Qualité de coupe et facteurs d'influence
La qualité de la découpe des plaquettes est essentielle pour le conditionnement ultérieur des puces, les tests, ainsi que pour les performances et la fiabilité globales du produit final. Les problèmes courants rencontrés lors de la découpe comprennent les fissures, l'écaillage et les écarts de coupe. Ces problèmes sont influencés par plusieurs facteurs qui interagissent.
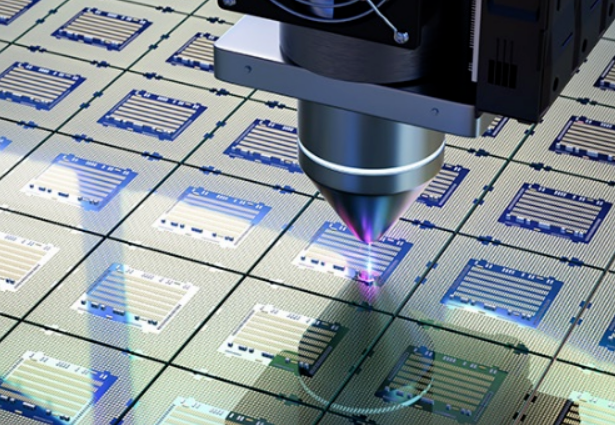
Catégorie | Contenu | Impact |
Paramètres du processus | La vitesse de coupe, l'avance et la profondeur de coupe influencent directement la stabilité et la précision du processus de coupe. Des réglages incorrects peuvent entraîner une concentration de contraintes et une zone affectée thermiquement excessive, provoquant fissures et écaillages. Un ajustement approprié des paramètres en fonction du matériau de la plaquette, de son épaisseur et des exigences de coupe est essentiel pour obtenir les résultats de coupe souhaités. | Les paramètres de processus appropriés garantissent une coupe précise et réduisent le risque de défauts tels que les fissures et les écaillages. |
Facteurs d'équipement et de matériel | -Qualité de la lameLe matériau, la dureté et la résistance à l'usure de la lame influencent la fluidité de la coupe et la planéité de la surface. Des lames de mauvaise qualité augmentent la friction et les contraintes thermiques, ce qui peut entraîner des fissures ou des écaillages. Le choix du bon matériau de lame est crucial. -Performances du liquide de refroidissementLes liquides de refroidissement contribuent à réduire la température de coupe, à minimiser les frottements et à éliminer les débris. Un liquide de refroidissement inefficace peut entraîner des températures élevées et une accumulation de débris, ce qui affecte la qualité et l'efficacité de la coupe. Il est donc essentiel de choisir des liquides de refroidissement efficaces et respectueux de l'environnement. | La qualité de la lame affecte la précision et la fluidité de la coupe. Un liquide de refroidissement inefficace peut nuire à la qualité et à l'efficacité de la coupe, d'où la nécessité d'une utilisation optimale du liquide de refroidissement. |
Contrôle des processus et inspection de la qualité | -Contrôle des processus:Surveillance et réglage en temps réel des paramètres de coupe clés pour garantir la stabilité et la cohérence du processus de coupe. -Contrôle de la qualité:Les contrôles d'apparence après découpe, les mesures dimensionnelles et les tests de performances électriques aident à identifier et à résoudre rapidement les problèmes de qualité, améliorant ainsi la précision et la cohérence de la découpe. | Un contrôle de processus et une inspection de qualité appropriés contribuent à garantir des résultats de coupe cohérents et de haute qualité et une détection précoce des problèmes potentiels. |

Améliorer la qualité de coupe
L'amélioration de la qualité de découpe nécessite une approche globale prenant en compte les paramètres de procédé, le choix des équipements et des matériaux, le contrôle et l'inspection des procédés. En perfectionnant continuellement les technologies de découpe et en optimisant les méthodes de fabrication, la précision et la stabilité de la découpe des plaquettes peuvent être encore améliorées, offrant ainsi un support technique plus fiable à l'industrie de la fabrication de semi-conducteurs.
#03 Manipulation et tests après découpe
3.1 Nettoyage et séchage
Les étapes de nettoyage et de séchage après la découpe des plaquettes sont essentielles pour garantir la qualité des puces et le bon déroulement des processus ultérieurs. Lors de cette étape, il est essentiel d'éliminer soigneusement les débris de silicium, les résidus de liquide de refroidissement et autres contaminants générés lors de la découpe. Il est également important de veiller à ce que les puces ne soient pas endommagées pendant le nettoyage et, après le séchage, à ce qu'il ne reste aucune humidité à la surface de la puce afin d'éviter des problèmes tels que la corrosion ou les décharges électrostatiques.
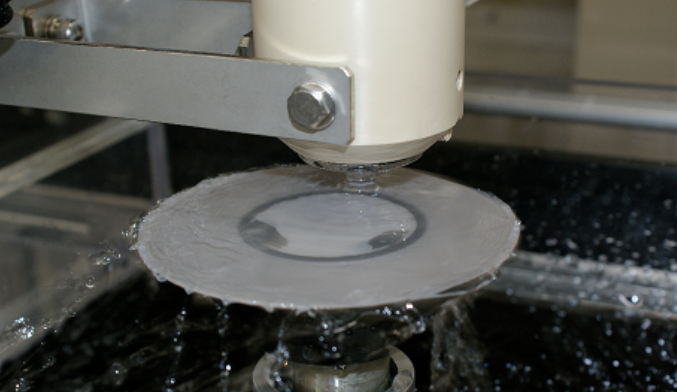
Traitement après découpe : processus de nettoyage et de séchage
Étape du processus | Contenu | Impact |
Processus de nettoyage | -Méthode:Utilisez des agents de nettoyage spécialisés et de l'eau pure, combinés à des techniques de brossage ultrasonique ou mécanique pour le nettoyage. | Assure l'élimination complète des contaminants et évite d'endommager les copeaux lors du nettoyage. |
-Sélection d'agent de nettoyage: Choisissez en fonction du matériau de la plaquette et du type de contaminant pour garantir un nettoyage efficace sans endommager la puce. | Une sélection appropriée de l'agent est essentielle pour un nettoyage efficace et une protection contre les copeaux. | |
-Contrôle des paramètres:Contrôlez strictement la température, le temps et la concentration de la solution de nettoyage pour éviter les problèmes de qualité causés par un nettoyage inapproprié. | Les contrôles aident à éviter d’endommager la plaquette ou de laisser des contaminants, garantissant ainsi une qualité constante. | |
Processus de séchage | -Méthodes traditionnelles:Séchage à l'air naturel et séchage à l'air chaud, qui ont une faible efficacité et peuvent entraîner une accumulation d'électricité statique. | Peut entraîner des temps de séchage plus lents et des problèmes potentiels d'électricité statique. |
-Technologies modernes:Utilisez des technologies avancées telles que le séchage sous vide et le séchage infrarouge pour garantir que les puces sèchent rapidement et éviter les effets nocifs. | Processus de séchage plus rapide et plus efficace, réduisant le risque de décharge statique ou de problèmes liés à l'humidité. | |
Sélection et entretien de l'équipement | -Sélection de l'équipement:Les machines de nettoyage et de séchage hautes performances améliorent l'efficacité du traitement et contrôlent finement les problèmes potentiels lors de la manipulation. | Des machines de haute qualité garantissent un meilleur traitement et réduisent le risque d'erreurs lors du nettoyage et du séchage. |
-Entretien des équipements:L'inspection et l'entretien réguliers de l'équipement garantissent qu'il reste dans un état de fonctionnement optimal, garantissant la qualité des copeaux. | Un entretien approprié prévient les pannes d’équipement, garantissant un traitement fiable et de haute qualité. |
Nettoyage et séchage après découpe
Les étapes de nettoyage et de séchage après la découpe des plaquettes sont des processus complexes et délicats qui nécessitent une prise en compte rigoureuse de multiples facteurs pour garantir le résultat final. Grâce à des méthodes scientifiques et des procédures rigoureuses, il est possible de garantir que chaque puce franchisse les étapes de conditionnement et de test ultérieures dans des conditions optimales.
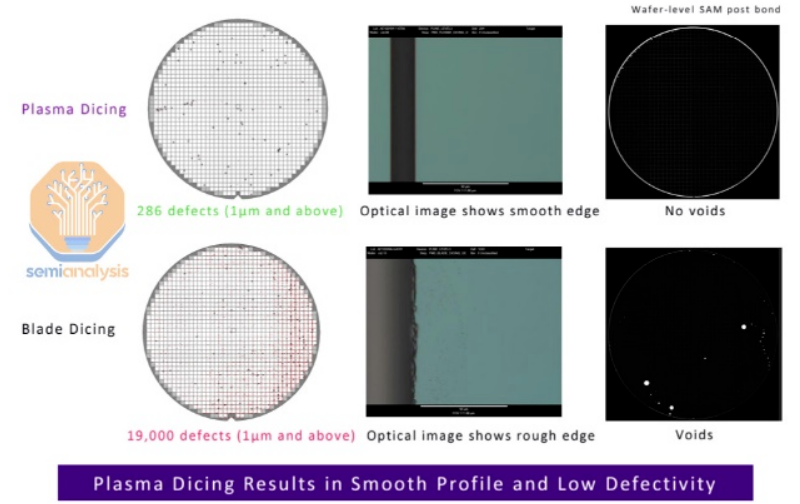
Inspection et tests après découpe
Étape | Contenu | Impact |
Étape d'inspection | 1.Inspection visuelleUtilisez un équipement d'inspection visuelle ou automatisé pour détecter les défauts visibles tels que les fissures, les écaillages ou la contamination à la surface des copeaux. Identifiez rapidement les copeaux physiquement endommagés pour éviter le gaspillage. | Aide à identifier et à éliminer les puces défectueuses au début du processus, réduisant ainsi les pertes de matière. |
2.Mesure de la taille:Utilisez des appareils de mesure de précision pour mesurer avec précision les dimensions des puces, en vous assurant que la taille de coupe répond aux spécifications de conception et en évitant les problèmes de performances ou les difficultés d'emballage. | Garantit que les puces respectent les limites de taille requises, évitant ainsi la dégradation des performances ou les problèmes d'assemblage. | |
3.Tests de performance électrique:Évaluez les paramètres électriques clés tels que la résistance, la capacité et l'inductance, pour identifier les puces non conformes et garantir que seules les puces qualifiées en termes de performances passent à l'étape suivante. | Garantit que seules les puces fonctionnelles et testées en termes de performances avancent dans le processus, réduisant ainsi le risque de défaillance dans les étapes ultérieures. | |
Étape de test | 1.Tests fonctionnels:Vérifiez que la fonctionnalité de base de la puce fonctionne comme prévu, en identifiant et en éliminant les puces présentant des anomalies fonctionnelles. | S'assure que les puces répondent aux exigences opérationnelles de base avant de passer aux étapes ultérieures. |
2.Tests de fiabilité:Évaluez la stabilité des performances de la puce dans le cadre d'une utilisation prolongée ou d'environnements difficiles, impliquant généralement un vieillissement à haute température, des tests à basse température et des tests d'humidité pour simuler des conditions extrêmes du monde réel. | Garantit que les puces peuvent fonctionner de manière fiable dans diverses conditions environnementales, améliorant ainsi la longévité et la stabilité du produit. | |
3.Test de compatibilité: Vérifiez que la puce fonctionne correctement avec d’autres composants ou systèmes, en vous assurant qu’il n’y a pas de défauts ou de dégradation des performances dues à une incompatibilité. | Assure un fonctionnement fluide dans les applications du monde réel en évitant les problèmes de compatibilité. |
3.3 Emballage et stockage
Après la découpe des plaquettes, les puces constituent un élément crucial du processus de fabrication des semi-conducteurs. Leur conditionnement et leur stockage sont donc tout aussi importants. Des mesures de conditionnement et de stockage appropriées sont essentielles non seulement pour garantir la sécurité et la stabilité des puces pendant le transport et le stockage, mais aussi pour assurer un soutien efficace aux étapes ultérieures de production, de test et de conditionnement.
Résumé des étapes d'inspection et de test :
Les étapes d'inspection et de test des puces après la découpe des wafers couvrent divers aspects, notamment l'inspection visuelle, la mesure de la taille, les tests de performances électriques, les tests fonctionnels, les tests de fiabilité et les tests de compatibilité. Ces étapes sont interconnectées et complémentaires, constituant une barrière solide pour garantir la qualité et la fiabilité du produit. Grâce à des procédures d'inspection et de test strictes, les problèmes potentiels peuvent être identifiés et résolus rapidement, garantissant ainsi que le produit final répond aux exigences et aux attentes du client.
Aspect | Contenu |
Mesures d'emballage | 1.Antistatique:Les matériaux d’emballage doivent avoir d’excellentes propriétés antistatiques pour empêcher l’électricité statique d’endommager les appareils ou d’affecter leurs performances. |
2.Résistant à l'humidité:Les matériaux d'emballage doivent avoir une bonne résistance à l'humidité pour éviter la corrosion et la détérioration des performances électriques causées par l'humidité. | |
3.Résistant aux chocs:Les matériaux d'emballage doivent fournir une absorption efficace des chocs pour protéger les puces des vibrations et des impacts pendant le transport. | |
Environnement de stockage | 1.Contrôle de l'humidité:Contrôlez strictement l'humidité dans une plage appropriée pour éviter l'absorption d'humidité et la corrosion causées par une humidité excessive ou des problèmes statiques causés par une faible humidité. |
2.Propreté: Maintenir un environnement de stockage propre pour éviter la contamination des puces par la poussière et les impuretés. | |
3.Contrôle de la température: Définissez une plage de température raisonnable et maintenez la stabilité de la température pour éviter un vieillissement accéléré dû à une chaleur excessive ou à des problèmes de condensation causés par de basses températures. | |
Inspection régulière | Inspectez et évaluez régulièrement les puces stockées, en effectuant des inspections visuelles, des mesures de taille et des tests de performance électrique afin d'identifier et de résoudre rapidement les problèmes potentiels. En fonction de la durée et des conditions de stockage, planifiez l'utilisation des puces afin de garantir leur utilisation dans des conditions optimales. |
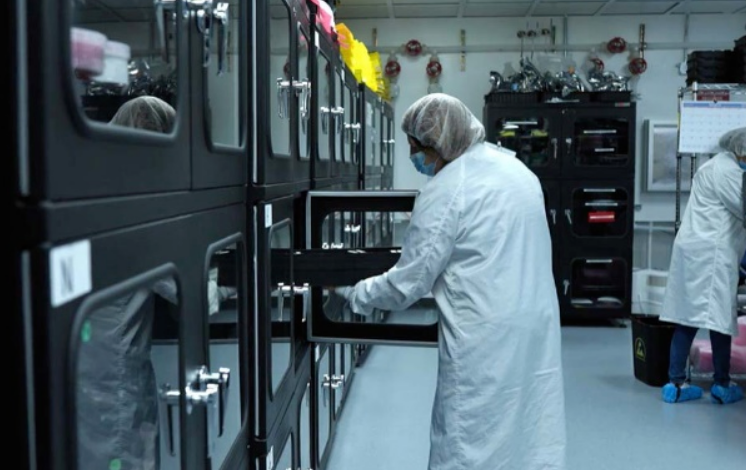
La problématique des microfissures et des dommages lors du découpage des plaquettes constitue un défi majeur dans la fabrication des semi-conducteurs. La contrainte de coupe est la principale cause de ce phénomène, car elle crée de minuscules fissures et dommages à la surface des plaquettes, ce qui entraîne une augmentation des coûts de fabrication et une baisse de la qualité des produits.
Pour relever ce défi, il est crucial de minimiser les contraintes de coupe et d'optimiser les techniques, les outils et les conditions de coupe. Une attention particulière portée à des facteurs tels que le matériau de la lame, la vitesse de coupe, la pression et les méthodes de refroidissement peut contribuer à réduire la formation de microfissures et à améliorer le rendement global du procédé. De plus, des recherches en cours sur des technologies de coupe plus avancées, comme le découpage au laser, explorent des moyens d'atténuer davantage ces problèmes.
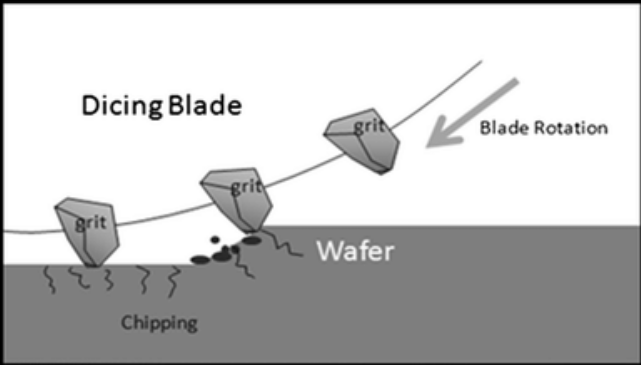
En tant que matériau fragile, les plaquettes sont sujettes à des modifications structurelles internes lorsqu'elles sont soumises à des contraintes mécaniques, thermiques ou chimiques, ce qui entraîne la formation de microfissures. Bien que ces fissures ne soient pas immédiatement visibles, elles peuvent s'étendre et causer des dommages plus importants à mesure que le processus de fabrication progresse. Ce problème devient particulièrement problématique lors des étapes ultérieures de conditionnement et de test, où les fluctuations de température et les contraintes mécaniques supplémentaires peuvent entraîner l'évolution de ces microfissures vers des fractures visibles, potentiellement responsables de la défaillance de la puce.
Pour atténuer ce risque, il est essentiel de contrôler soigneusement le processus de découpe en optimisant des paramètres tels que la vitesse, la pression et la température. L'utilisation de méthodes de découpe moins agressives, comme le découpage au laser, peut réduire les contraintes mécaniques sur la plaquette et minimiser la formation de microfissures. De plus, la mise en œuvre de méthodes d'inspection avancées, comme le balayage infrarouge ou l'imagerie par rayons X, pendant le découpage de la plaquette peut aider à détecter ces fissures précoces avant qu'elles n'aggravent les dommages.
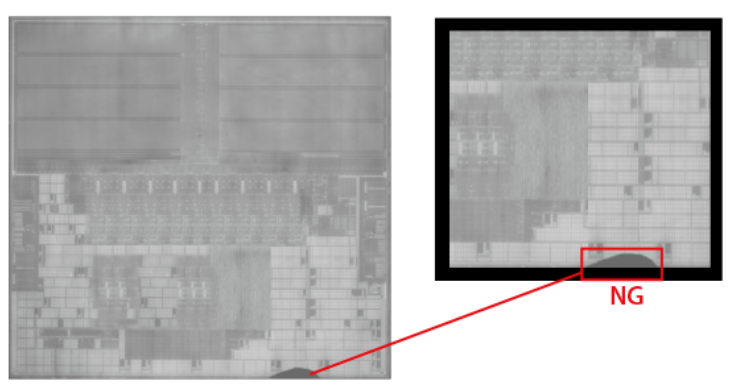
Les dommages à la surface des plaquettes constituent une préoccupation majeure lors du découpage en dés, car ils peuvent avoir un impact direct sur les performances et la fiabilité de la puce. Ces dommages peuvent être causés par une mauvaise utilisation des outils de coupe, des paramètres de coupe incorrects ou des défauts de matériau inhérents à la plaquette elle-même. Quelle qu'en soit la cause, ces dommages peuvent entraîner des altérations de la résistance électrique ou de la capacité du circuit, affectant ainsi les performances globales.
Pour répondre à ces problèmes, deux stratégies clés sont explorées :
1. Optimisation des outils et paramètres de coupe:En utilisant des lames plus tranchantes, en ajustant la vitesse de coupe et en modifiant la profondeur de coupe, la concentration de contraintes pendant le processus de coupe peut être minimisée, réduisant ainsi le risque de dommages.
2.Explorer de nouvelles technologies de coupeDes techniques avancées comme la découpe laser et plasma offrent une précision accrue tout en réduisant potentiellement les dommages infligés aux plaquettes. Ces technologies sont étudiées afin de trouver des moyens d'obtenir une précision de découpe élevée tout en minimisant les contraintes thermiques et mécaniques sur les plaquettes.
Zone d'impact thermique et ses effets sur les performances
Dans les procédés de découpe thermique tels que la découpe laser et plasma, les températures élevées créent inévitablement une zone d'impact thermique à la surface du wafer. Cette zone, où le gradient de température est important, peut altérer les propriétés du matériau et affecter les performances finales de la puce.
Impact de la zone affectée thermiquement (TAZ) :
Modifications de la structure cristallineÀ haute température, les atomes du matériau de la plaquette peuvent se réorganiser, provoquant des distorsions dans la structure cristalline. Cette distorsion fragilise le matériau, réduisant sa résistance mécanique et sa stabilité, ce qui augmente le risque de défaillance de la puce en cours d'utilisation.
Modifications des propriétés électriques:Les températures élevées peuvent altérer la concentration et la mobilité des porteurs dans les matériaux semi-conducteurs, affectant ainsi la conductivité électrique et l'efficacité de transmission du courant de la puce. Ces changements peuvent entraîner une baisse des performances de la puce, la rendant potentiellement inadaptée à son usage prévu.
Pour atténuer ces effets, le contrôle de la température pendant la découpe, l’optimisation des paramètres de découpe et l’exploration de méthodes telles que les jets de refroidissement ou les traitements de post-traitement sont des stratégies essentielles pour réduire l’étendue de l’impact thermique et maintenir l’intégrité du matériau.
Globalement, les microfissures et les zones d'impact thermique constituent des défis majeurs dans la technologie de découpage des plaquettes. La poursuite des recherches, ainsi que les avancées technologiques et les mesures de contrôle qualité, seront nécessaires pour améliorer la qualité des produits semi-conducteurs et renforcer leur compétitivité sur le marché.
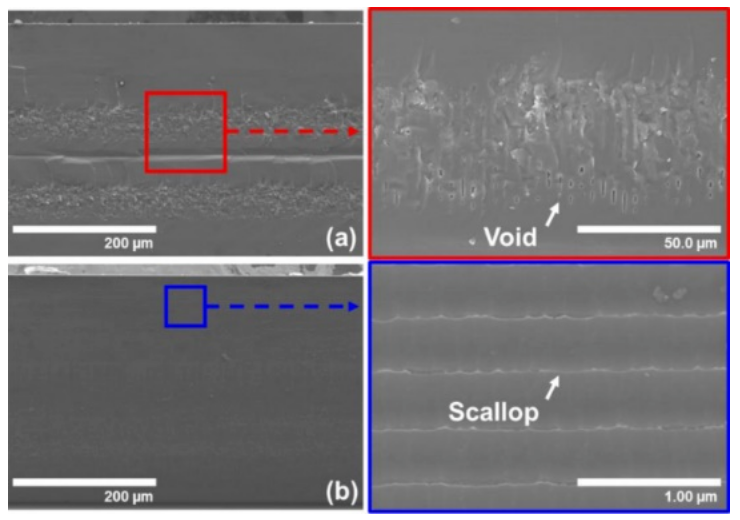
Mesures de contrôle de la zone d’impact thermique :
Optimisation des paramètres du processus de coupeRéduire la vitesse et la puissance de découpe permet de minimiser efficacement la taille de la zone d'impact thermique (ZAT). Cela permet de contrôler la quantité de chaleur générée pendant la découpe, ce qui a un impact direct sur les propriétés du matériau de la plaquette.
Technologies de refroidissement avancéesL'application de technologies telles que le refroidissement à l'azote liquide et le refroidissement microfluidique permet de limiter considérablement la portée de la zone d'impact thermique. Ces méthodes de refroidissement permettent de dissiper la chaleur plus efficacement, préservant ainsi les propriétés du matériau de la plaquette et minimisant les dommages thermiques.
Sélection des matériauxLes chercheurs explorent de nouveaux matériaux, tels que les nanotubes de carbone et le graphène, qui possèdent une excellente conductivité thermique et une excellente résistance mécanique. Ces matériaux peuvent réduire la zone d'impact thermique tout en améliorant les performances globales des puces.
En résumé, bien que la zone d'impact thermique soit une conséquence inévitable des technologies de découpe thermique, elle peut être efficacement maîtrisée grâce à des techniques de traitement et un choix de matériaux optimisés. Les recherches futures se concentreront probablement sur l'optimisation et l'automatisation des procédés de découpe thermique afin d'obtenir un découpage des plaquettes plus efficace et plus précis.

Stratégie d'équilibre :
Trouver l'équilibre optimal entre rendement des plaquettes et efficacité de production est un défi permanent dans la technologie de découpage de plaquettes. Les fabricants doivent prendre en compte de multiples facteurs, tels que la demande du marché, les coûts de production et la qualité des produits, afin d'élaborer une stratégie de production et des paramètres de processus rationnels. Parallèlement, l'introduction d'équipements de découpe avancés, l'amélioration des compétences des opérateurs et le renforcement du contrôle qualité des matières premières sont essentiels pour maintenir, voire améliorer, le rendement tout en augmentant l'efficacité de la production.
Défis et opportunités futurs :
Avec les progrès de la technologie des semi-conducteurs, la découpe de plaquettes est confrontée à de nouveaux défis et opportunités. Avec la réduction de la taille des puces et l'augmentation de l'intégration, les exigences en matière de précision et de qualité de découpe augmentent considérablement. Parallèlement, les technologies émergentes offrent de nouvelles perspectives pour le développement des techniques de découpe de plaquettes. Les fabricants doivent rester attentifs à la dynamique du marché et aux tendances technologiques, en ajustant et en optimisant en permanence leurs stratégies de production et leurs paramètres de processus afin de répondre aux évolutions du marché et aux exigences technologiques.
En conclusion, en intégrant les considérations de la demande du marché, des coûts de production et de la qualité des produits, et en introduisant des équipements et des technologies de pointe, en améliorant les compétences des opérateurs et en renforçant le contrôle des matières premières, les fabricants peuvent atteindre le meilleur équilibre entre le rendement des plaquettes et l'efficacité de la production lors du découpage des plaquettes, conduisant à une production de produits semi-conducteurs efficace et de haute qualité.
Perspectives d'avenir :
Grâce aux avancées technologiques rapides, la technologie des semi-conducteurs progresse à un rythme sans précédent. Étape cruciale de la fabrication des semi-conducteurs, la découpe de plaquettes est vouée à de nouveaux développements prometteurs. À l'avenir, elle devrait permettre des améliorations significatives en termes de précision, d'efficacité et de coûts, insufflant ainsi un nouveau dynamisme à la croissance continue de l'industrie des semi-conducteurs.
Augmentation de la précision :
Dans la quête d'une précision accrue, la technologie de découpe de plaquettes repoussera sans cesse les limites des procédés existants. L'étude approfondie des mécanismes physiques et chimiques du procédé et le contrôle précis des paramètres de découpe permettront d'obtenir des résultats de découpe plus précis, répondant ainsi à des exigences de conception de circuits de plus en plus complexes. De plus, l'exploration de nouveaux matériaux et de nouvelles méthodes de découpe améliorera considérablement le rendement et la qualité.
Améliorer l'efficacité :
Les nouveaux équipements de découpe de plaquettes privilégieront une conception intelligente et automatisée. L'introduction de systèmes de contrôle et d'algorithmes avancés permettra aux équipements d'ajuster automatiquement les paramètres de découpe pour s'adapter aux différents matériaux et exigences de conception, améliorant ainsi considérablement l'efficacité de la production. Des innovations telles que la technologie de découpe multi-plaquettes et les systèmes de remplacement rapide des lames joueront un rôle crucial dans l'amélioration de l'efficacité.
Réduire les coûts :
La réduction des coûts est un axe clé du développement des technologies de découpe de plaquettes. Le développement de nouveaux matériaux et de nouvelles méthodes de découpe devrait permettre de maîtriser efficacement les coûts d'équipement et de maintenance. De plus, l'optimisation des processus de production et la réduction des taux de rebut permettront de réduire encore davantage les déchets lors de la fabrication, entraînant ainsi une baisse des coûts de production globaux.
Fabrication intelligente et IoT :
L'intégration de la fabrication intelligente et des technologies de l'Internet des objets (IoT) transformera profondément la technologie de découpe de plaquettes. Grâce à l'interconnectivité et au partage de données entre les appareils, chaque étape du processus de production peut être surveillée et optimisée en temps réel. Cela améliore non seulement l'efficacité de la production et la qualité des produits, mais offre également aux entreprises des prévisions de marché plus précises et une aide à la décision.
À l'avenir, la technologie de découpe de plaquettes réalisera des progrès remarquables en termes de précision, d'efficacité et de coût. Ces avancées stimuleront le développement continu de l'industrie des semi-conducteurs et apporteront davantage d'innovations technologiques et de commodités à la société.
Date de publication : 19 novembre 2024